The production of bollards typically involves several processes, including designing, cutting, welding, and finishing. First, the bollard's design is created, and then the metal is cut using techniques such as laser cutting or sawing. Once the metal pieces are cut, they are welded together to form the shape of the bollard. The welding process is essential to ensure the bollard's strength and durability. After welding, the bollard is finished, which can include polishing, painting, or powder coating, depending on the desired look and function. The finished bollard is then inspected for quality and shipped to the customer.
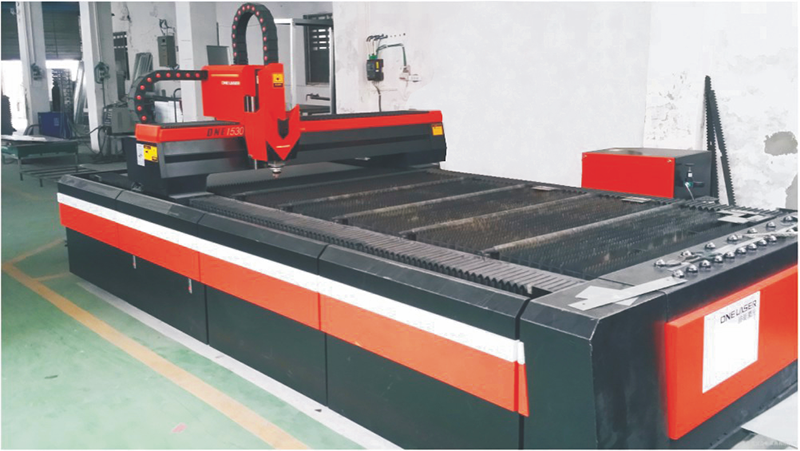
Laser Cutting:
Laser cutting technology has revolutionized the manufacturing industry in recent years, and it has found its way into the production of bollards. Bollards are short, sturdy posts used to direct traffic, prevent vehicle access, and protect buildings from accidental collisions.
Laser cutting technology uses a high-powered laser beam to cut materials with precision and speed. This technology has numerous advantages over traditional cutting methods, such as sawing or drilling. It allows for cleaner, more precise cuts and can easily handle intricate designs and patterns.
In the production of bollards, laser cutting technology is used to create the bollard's shape and design. The laser is directed by a computer program, allowing for precise cuts and shaping of the metal. The technology can cut through a range of materials, including steel, aluminum, and brass, allowing for a variety of options in bollard design.
One of the major advantages of laser cutting technology is its ability to work quickly and efficiently, allowing for mass production of bollards. With traditional cutting methods, it can take hours or even days to produce a single bollard. With laser cutting technology, dozens of bollards can be produced in a matter of hours, depending on the complexity of the design.
Another advantage of laser cutting technology is the precision it offers. The laser beam can cut through metal with a thickness of up to several inches, allowing for the creation of sturdy, reliable bollards. This precision also allows for intricate designs and patterns, giving bollards a sleek and modern look.
In conclusion, laser cutting technology has become an essential tool in the production of bollards. Its precision, speed, and versatility make it an ideal choice for manufacturers looking to create sturdy, reliable, and visually appealing bollards. As the manufacturing industry continues to evolve, laser cutting technology will undoubtedly play an increasingly important role in the production of a wide range of products.
Welding:
Welding is an essential process in the production of bollards. It involves joining metal pieces together by heating them to a high temperature and then allowing them to cool, resulting in a strong and durable bond. In the production of bollards, welding is used to connect the metal pieces together to form the bollard's shape and structure. The welding process requires a high level of skill and precision to ensure the welds are strong and reliable. The type of welding used in bollard production may vary depending on the materials used and the desired strength and durability of the finished product.
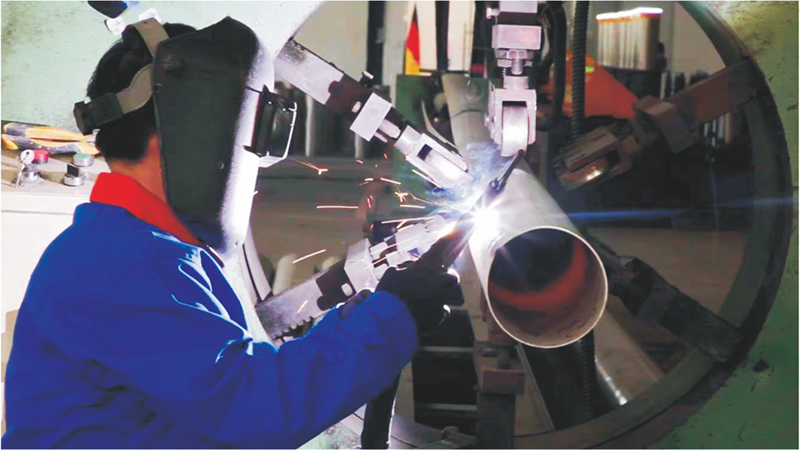
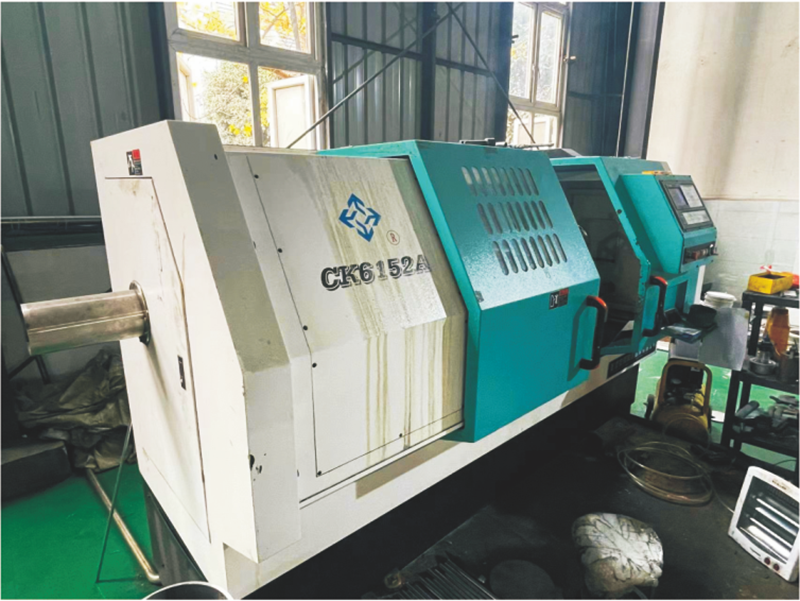
Polishing :
The polishing process is an important step in the production of bollards. Polishing is a mechanical process that involves the use of abrasive materials to smooth the surface of the metal and remove any imperfections. In bollard production, the polishing process is typically used to create a smooth and shiny finish on the bollard, which not only enhances its appearance but also helps to protect it from rust and other forms of corrosion. The polishing process can be done manually or by using automated equipment, depending on the size and complexity of the bollard. The type of polishing material used may also vary depending on the desired finish, with options ranging from coarse to fine abrasives. Overall, the polishing process plays a critical role in ensuring that the finished bollard meets the required quality and appearance standards.
CNC:
In the manufacturing industry, the use of CNC (Computer Numerical Control) machining technology has become increasingly popular due to its numerous advantages over traditional manufacturing methods. This technology has found its way into the production process of security products, including bollard,safes,and security doors. The precision and accuracy of CNC machining offer several benefits in the production process of security products, including increased efficiency, cost savings, and higher-quality finished products.
Powder coating :
Powder coating is a popular finishing technology used in the production of bollards. It involves applying a dry powder to the surface of the metal and then heating it to form a durable and protective layer. Powder coating technology offers several advantages over traditional painting methods, including greater durability, resistance to chipping and scratching, and the ability to create a range of colors and finishes. In the production of bollards, powder coating is typically applied after the welding and polishing processes are complete. The bollard is first cleaned and prepared to ensure that the powder coating adheres properly to the surface. The dry powder is then applied using a spray gun, and the bollard is heated to form a smooth and durable finish. Powder coating technology is a popular choice in bollard production due to its durability and ability to create a consistent and high-quality finish.
